Increasingly we are living with the results of our collective lethargy on carbon management - rising temperatures, extreme weather events, and dwindling resources.
For time immemorial we’ve taken natural resources and, increasingly processed them, and erected shelters and infrastructure. And we have all seen the key data. The built environment – from homes and offices, to factories and bridges – now accounts for more than a quarter of all greenhouse gas emissions, and close to 40%, (14.4 gigatons) of the worlds carbon dioxide (CO2) emissions annually. That’s equivalent to emissions from 8 billion (non-electric) vehicles (around five times as many cars as exist today) or, conversely, carbon that would be preserved by 9 million wind turbines.
Annual cuts in emissions globally are required at a rate of 3%-7% per year if the Paris Agreement targets are to be met and, according to the United Nations Framework Convention on Climate Change (UNFCC), the emissions gap to limit global warming to 2% in 2030 is 12-15 gigatons of CO2 – a goal curiously analogous with the annual emissions created by the construction industry.
So, one immediate (but impractical and unviable) solution to the worlds environmental challenges is to simply stop construction.
However, construction is a huge economic contributor, employing millions and touching all aspects of human life. We have heard the calls for change, but is it inherently logical that the construction industry would be a large consumer of carbon given its scale and importance to human existence on this planet? Incremental progress is being achieved with new materials, building performance and measurement, and cleaner energy. So why is the construction industry, once synonymous with progress and development, now at the precipice of a daunting new frontier which many are oblivious to?
Here are five good reasons why.
- The Spotlight is turning on Construction.
It is illuminating when we consider carbon intensity action and progress in context with the energy sector over the last decade. As the largest polluter, and with available technologies and large potential reductions in carbon intensity, regulators and investors have gone after the power industry with a two-pronged assault to improve efficiency (thus reducing demand), and scale up renewables, endeavouring to progressively replace the worlds fossil fuels energy mix. In recent years, the energy sector initiatives have stepped up, amplifying the achievements. In comparison material circularity in construction has declined more than 30% percent in the last 5 years due to large waste streams from rapid urbanisation and growing populations, both of which are increasing the extraction rates and use of materials using unchanged analogue processing and consumption.
More pointedly, in the coming years the power industry will have achieved around 65% of the targeted reductions, with its remaining emissions around the same level as other major emitting industries. Further carbon reductions will become incremental and harder, the attention must, and will turn to the next largest emitters – transport and construction.
There is a template in the spotlight and, similarly, we must expect regulators will take a dual approach to construction, aimed at both improving efficiencies (with carbon certified supply chain, high-yield construction waste, lower-carbon substitute materials and various options for storing CO2 in materials production, and technology led optimisation and material innovation), and reducing demand (with material circularity and multiple version of recycled buildings).
- Material Efficiency and Circular Transition will be mandatory.
One third of all CO2 emissions across the globe result from extracting, processing, and using materials. For an industry that wastes around 30% of that material, using technology, circularity, and off-site manufacturing to improve material efficiency by, even, 5-10% is entirely plausible and within reach today. This alone could account for a reduction in CO2 emissions in the order of five hundred million tons per annum.
The annual meeting of the World Economic Forum in 2024 found that demand for low carbon buildings could be three times higher than supply, and a recent white paper demonstrates that circular approaches for materials such as cement, steel, aluminium, and gypsum could abate 75% of embodied emissions in the built environment.
Consideration of circular transition, therefore, must be one of the major paradigm shifts in construction. A continuing challenge for scaling circular solutions stems from a lack of transparency and education, on both the value chain, however given the potential impact and gain, we can expect regulators and policy makers to reward and incentivise circularity at the commodity and compliance levels.
- Climate change litigation will force behaviour change.
Climate change litigation continues to grow in importance year-on-year and in the southern hemisphere, with the role of litigation in affecting “the outcome and ambition of climate governance” being recognised by the Intergovernmental Panel on Climate Change (IPCC). To date, construction has been relatively ‘unscathed’ with most cases filed against governments, fossil fuel companies, food and agriculture, transport, plastics and finance, however litigants increasingly appear to draw a connection between public debate about the contribution that consumer and lifestyle choices can make to reducing emissions, and widespread concern that industry misinformation and inaction may prevent such choices being enabled. It is inherently likely, perhaps inevitable, that other high emitting sectors including construction and associated heavy-duty industry participants, that have failed to prepare for climate change, may be the next targets for litigants.
- The ‘inevitable’ carbon border tax
Somewhere, in some form, a cap-and-trade scheme will be implemented - in which companies must procure permits for emissions, which they in turn trade amongst themselves or use to offset emissions in the deep complex value chain associated with construction industry.
In the past, governments who have followed this course have confronted a fundamental problem that arises where, in the absence of a global carbon price, local industry is penalised by dislocated competitors who can produce at lower costs.
It follows that functioning emissions ‘carrot and stick’ schemes need a means of adjustment at the border to make sure imports and domestic production are treated similarly. This makes carbon border tax a necessity to prevent “carbon leakage” - where measures to reduce emissions in one country led producers to relocate to another with less ambitious climate regulation. In all, 27 countries now have carbon border tax policy implemented, including for example Canada, the United Kingdom, Singapore, France, Norway, Denmark, Finland, Switzerland and Sweeden.
In recent years, carbon border tax policy has left its mark on global discussions about trade and climate change. On the one hand by putting a price on carbon, it discourages emissions. However, as a trade-related measure, it affects production and exports and contrarians argue that it will raise the administrative burden of crossing borders and increase trade frictions, especially for small businesses – reducing choice and raise costs for consumers.
However, in parallel with other policy and regulation, as a device to equalise and record decarbonisation and its associated costs, it is almost inevitable that a border tax scheme be introduced in the future – albeit likely phased to give business time to adjust but also provide an ironclad commitment to reduce the incentive for production to gradually relocate elsewhere.
- Carbon reduction solutions must be integrated.
According to McKinsey analysis, renewable energy is about four times more expensive to transport in bulk as it is to generate. As an island nation that means, at a foundation level, ‘hard to abate’ emissions are likely to persist in the medium term as Australia’s industry customers are unlikely to import as much green energy as needed to make significant and quick change.
More widely, whilst a number of countries that have pledged to achieve net zero emissions now account for two-thirds of global emissions of CO2, the pledges to date would still leave around 22 billion tonnes of CO2 to be mitigated. Accordingly, the IPCC has made it clear that, whilst reducing carbon is the priority response to climate change, carbon dioxide removal (CDR) is a critical tool for neutralising residual emissions and achieving net zero because these technologies can be useful to offset residual emissions once businesses have exhausted all carbon reduction efforts. Now, most scenarios aligned with the Paris Agreement propose and project substantial CDR capacities, with an expected 6-10 gigatons per annum being required.
CDR can be especially pertinent for those emissions that are technologically or economically prohibitive to reduce and, given CDR’s potential importance therefore, removals must become a routine consideration for the construction industry in the future to claim they have reached net zero.
Whilst the CDR industry is currently immature, and trading at unaffordable prices, investment will significantly increase in the coming years. MacKinsey estimate the cumulative investment in CDR required to deliver net zero in 2050 to be at least $6 trillion, with CDR costs plummeting in the coming years and estimated to decline up to 60% by 2030.
The construction industry with its expertise and resources could and should, for example, be positioning itself for partnerships and investment in CDR initiatives and schemes which could sensibly include wetland and peatland restoration, blue carbon management, biochar, biomass and enhanced weathering solutions.
For the construction industry, the time to get organised is now. The consequences, and the opportunities, could not be higher, and the impact of continued lethargy and inaction are extremely dire. We need to rise to this challenge, not as adversaries or competitors, but as stewards of the earth—united in a commitment to building a brighter, more sustainable future.
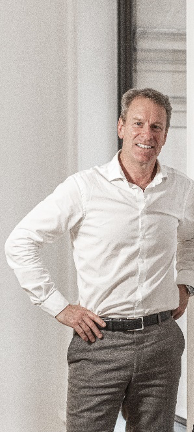
Gavin Tonnet is a recognised expert and leader in property development and technology, both in Australia and around the world having created and led businesses for Mirvac, Leighton, Stockland, Japanese giant, Sekisui House, and proptech start-ups, Donovan Group and utecture. He was responsible for many significant city-changing urban renewal projects in Australia.